Warehouse Labelling - Top Tips and Best Practise
- lwhittle7
- Aug 4, 2020
- 3 min read
When undertaking a WMS project, the initial focus is always on the software, it's functionality and whether it's a good fit and delivers the benefits for the business - which is of course the most important place to start. Second comes the selection of the equipment, including label printers and hand-held scanning terminals, however, often forgotten, or definitely an afterthought, is the labelling of the locations in the warehouse. In actual fact, this should be given as much consideration as the selection of the equipment itself, to avoid problems with scanning once the system goes live.
Let's take a look at some of the important considerations as to why this should be the case:
Location Label Types
For warehouse racking, you will need to consider shelf edge labels that contain a barcode and human readable, identifying the location it is assigned to in the WMS. The height of the racking and how operators pick from the racking, will determine whether you need to label the high bay levels or use a multi-level labelling solution, as well as the type of handheld device you will need.
For example, if you are using man-up trucks, you will need single location labels on every level as they will need to be scanned by the worker at eye level. If you are using reach trucks, then you will need a multi-level location label at the lower levels, as the worker will not be at the same level as the goods or pallet. Arrows and colours indicate the level the location the barcode refers to, which aids identifying the correct higher level bays from the ground level without the need for an extended range scanner.
Of course not all stock will be stored in nice neat racking locations. You could use floor stacked areas, which would need either overhead suspended location barcodes or floor mounted plates.
Overhead plates displaying large barcodes and himan readables, can be suspended from wires or attached to overhead beams or trunking, so that they can be seen and scanned from ground level using extended range barcode scanners, such as the Zebra MC3300 or MC9300, as opposed to the Zebra TC7X PDA style terminal, which only scans at shorter ranges. Floor plates are a popular choice, but can be expensive due to the need for very rugged construction and installation to cope with heavy foot fall and fork truck traffic and often uneven surfaces.
Barcode Type, Size and Readability
Before you crack on and order all the locations barcodes and fit them, take some time to test and verify that they can be read by the equipment you will be using in the warehouse. For example, don't expect to be able to read small barcodes from a distance just because you use extended range scanning devices. The scanning device and the barcode type and size need to be matched up for perfect scanning. Frustration soon sets in when operators have difficulties reading the barcodes, leading to poor perception of the system and occasionally mis-use.
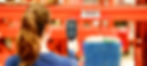
As a general rule, the larger and the bigger the barcode, the easier it is to scan. Consider the distances you will need to scan from, e.g. from sitting in the fork truck, on foot, etc. The label material used can also have a bearing on readability, as reflective material will provide better "scanability" and distance for example and is often used for overhead suspended barcodes.
Take all these points into account and you won't go far wrong, or better still simply ask us to advise! We have a wealth of experience in implementing warehouse management systems, and are able to provide everything from a full, in-house written WMS solution, to the data capture hardware to run your chosen WMS software on, or simply recommend and supply racking labels for your locations. Contact us on 01200 441977 or e-mail sales@barcode-it.co.uk